What do Locomotives and Injection Molding Machinery have in Common?
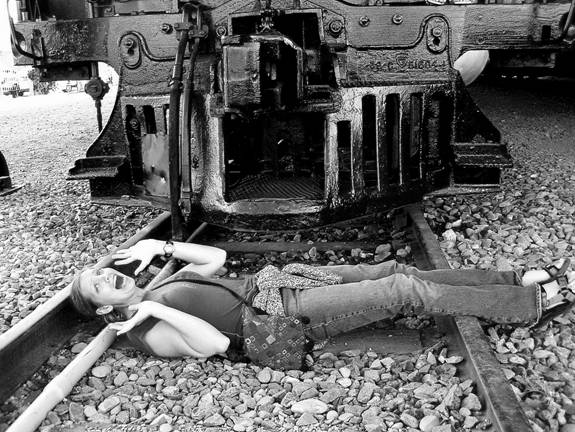
Well, to start with; pistons and cylinders, pressure and heat, dirt, maintenance and a lot of money. Both have experienced extensive technology changes as well. Steam locomotives became operational in about 1804. The diesel electric locomotive was patented in about 1912. A few years later it became operational. Hydraulic injection molding machines became widely used in the forties and made the transition to electric in the eighties.
In 1955 I was stopped at a railroad crossing in Riverside, California. We were on a family vacation. My brother shouted, “Look, there’s a Steam Engine!”
The huge black mass slowly passed. My dad said, “That is probably the last working steam engine you will ever see.” He was right.
The similarities in the transition from steam locomotives to diesel electric and from hydraulic presses to all electric injection molders are striking.
In 1955 almost all locomotives in the U.S had been converted to diesel electric. Arizona Eastern Atchison Topeka was one of the last to convert. Their president preferred steam. He said it was easier to work on, cheaper, tried and proven. His main reason was that he could clearly understand every component on it. Invisible electricity was a mystery. Finally he caved in and bought his first three diesel electrics. A week later they overheated while climbing the summit, caught fire and burnt to a pile of worthless charred debris. A steam engine had to haul them off. So for the next twelve years AEAT Rail Road continued to use steam.
The transition to electric presses is slow for many of the same reasons. In 2006 electrics amounted to only 44% of U.S. sales. In Asia they were 90%. In Europe they were only 8%. Europe’s hesitation is surprising. Their energy is expensive and European engineers usually prefer complex designs.
Lets look at the similarities in a change from hydraulic presses to electric and see how they compare to switching from steam to diesel electric.
Costs - Electric presses remain more expensive than hydraulics, but they are definitely cheaper to operate. Energy savings are most dramatic when comparing an older hydraulic machine. The newer hydraulics with variable volume pumps are more efficient. Maintenance and housekeeping are also areas of significant savings. Material consumption is often overlooked, but it is another area of significant savings. Due to the repeatability of part density, electric presses can get by with smaller shot sizes. The part density has a much narrower variance. So it is safer to use a smaller shot.
The following is a typical example of costs with an electric machine compared with a hydraulic machine. The hydraulic machine in this example has variable output pumps. If it had the older technology constant output pumps the energy savings would be even greater. The purpose of this study was to compare technology, not manufacturers. Both manufacturers make excellent machines.
Hydraulic machine - 1994 Van Dorn 300 ton toggle with variable output pumps and Pathfinder control.
Electric machine - 2006 Sumitomo SE350HD
|
|
Annual savings: | | |
Energy, at 8.3 cents / kwh | $ 5,985 | |
Material | $ 1,876 | |
Maintenance | $ 3,820 | |
House Keeping | $ 1,250 | |
Total | $ 12,931 | |
In addition to the above savings, many Utah manufacturers would qualify for an energy rebate, which in this case would amount to over three thousand dollars per year.
Maintenance - Having spent several years in the field of process and motor control, I’ve observed that many talented maintenance personnel feel more comfortable with hydraulics than electricity. This is probably because hydraulics can be seen. Electricity is invisible.
The same situation existed with steam locomotives and diesel electrics. Steam engines were totally understandable and easy to repair. Even a child could comprehend their operation. Many of the parts, such as babbitt bushings could be made and replaced in the field.
Fortunately, with a little training electric molding machines are as easy if not easier to repair than hydraulic. Trouble-shooting screens often point precisely to the problem, for example a burnt out heater, shorted sensor, or blown fuse. Flow diagrams in the manuals assist in isolating malfunctions. Printed circuit boards are easy to access, remove and replace. Major repairs are also easier. One maintenance technician reports that it takes eleven hours to replace a hydraulic motor, but only four hours to replace a ball screw.
Electric machines facilitate factory phone help. A maintenance specialist speaking on the phone with the factory technician can look at diagnostic light emitting diodes (LEDs) on specific boards and isolate the problem. If the manufacturer of your injection molding machine does not offer free and prompt technical assistance over the phone, buy a different brand next time.
 |
LED pilot lights facilitate troubleshooting |
Cleanliness - How many times have you heard, “There is no oil with electric presses.”? Well, that is simply not true. There is still oil for lubrication. With grease cartridges and proportional flow manifolds there shouldn’t be as much mess, and there obviously won’t be puddles of hydraulic oil on the floor, but there is still some oil.
It is argued that electric machines with water cooling are cleaner than fan cooled machines. Fans, they claim stir up dust. This is true if the machines have belt drives. Belts are the single major source of contamination in molding clean rooms. A better approach would be to use direct-coupled motors without belts and use fans to cool. Water cooling is messy, takes up room and adds numerous additional components to be serviced.
Performance - In many applications the main reason for selecting electric machines is performance. There is no question about it. Heat, pressure and time can be controlled more accurately and repeatably with electricity than hydraulics. Repeatability is consequently improved with all electric presses. Cycle time is reduced by simultaneous operations. Ejectors and other process functions have greater flexibility and accuracy.
Speed - In most but not all applications electric machines are faster. Traditionally one exception has been thin wall molds. Thin wall applications are usually molded with a hydraulic machine equipped with an accumulator. Sumitomo has gotten around this by manufacturing a high torque drive. It achieves the same pressures and speeds as a hydraulic or hybrid machine. As you might expect the motor is much larger in diameter. It looks almost like a brake rotor. Sumitomo makes their own drives.
Housekeeping - The elimination of hydraulic oil removes the necessity of periodic oil cleaning and replacement. Obviously the initial oil cost and disposal cost are eliminated as well. Other advantages include the elimination of heat exchangers and their routine cleaning.
Summary - Will hydraulic machines ever be eliminated entirely? It is doubtful. Traditionally linear movements have been accomplished better with cylinders and rotary movements with electric drives. With new technology these difficulties have been largely overcome, but there are still some areas where hydraulics are preferable. The most obvious is with core-pulls. Some core-pull applications can be accomplished with electric servos or pneumatics, but most require hydraulics. Another application where hydraulics is preferred is where high nozzle contact force is essential. This is an example of where linear movements can be done easier with hydraulics. The extreme nozzle contact pressures required, in some applications can only be provided by hydraulic cylinders. Fortunately self-contained hydraulic systems have been developed in recent years. These systems are closed and sealed. They require no maintenance, oil changes, filter changes, heat exchangers, etc. Very large hydraulic presses remain more economical than electrics.